XVT-2626 solves sticking issues in the forming line
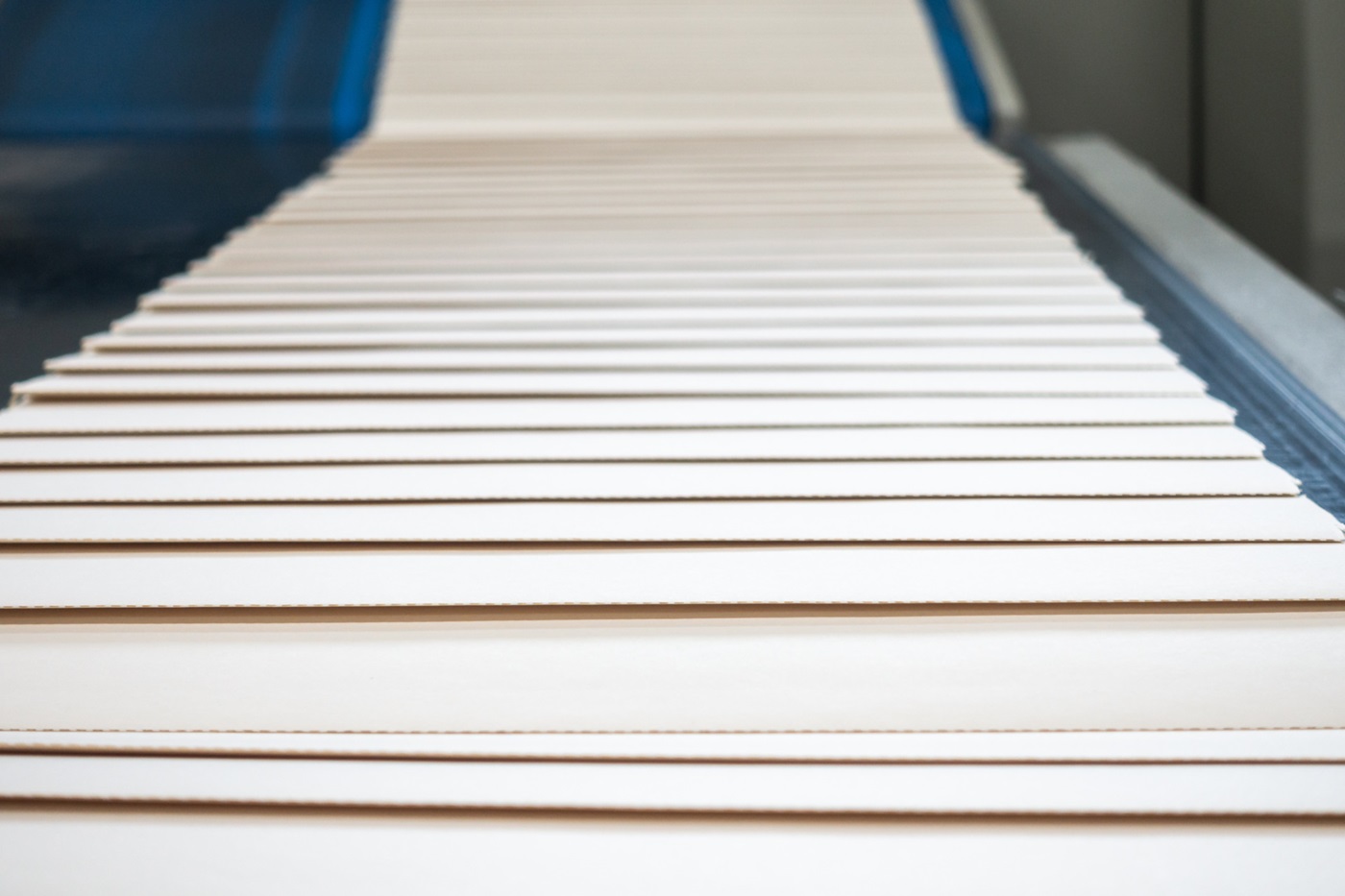
A producer of panel boards was experiencing sticking wood material on the belt of their forming line. The customer was obliged to stop production to clean the belt surface often. Such material residues, if not removed, would have compromised the finish and quality of the panel. In the areas of permanent dirt, the panel would have shown material defi ciencies. At this point, the panel had to be reworked and lead to a reduction in productivity.
The MDF producer was looking for an alternative belt with superior cleanability. Wooden particles must not stick to the belt as it would cause a decrease of lifetime of the belt.
11 months after the installation the belt as a trial the results have been satisfying. The customer has not been experiencing the same sticking issues they had in the forming line in the past. Furthermore, the main advantage seen by the customer is that the belt surface does not need to be cleaned as often. With the new XVT-2626, the customer saves on maintenance time each month translating into an increase in productivity of around 0.8 to 1%.
The customer no longer needs to clean the surface of the belt at each production change. In addition, the greater cleanliness of the surface has made it possible to reduce the number of discarded panels due to surface non-compliance.