Efficient lever and guide rail design beat slower, less accurate hot press
The PF-80/US hot pressing tool reduced joining time for over $4k in production savings, per minute.
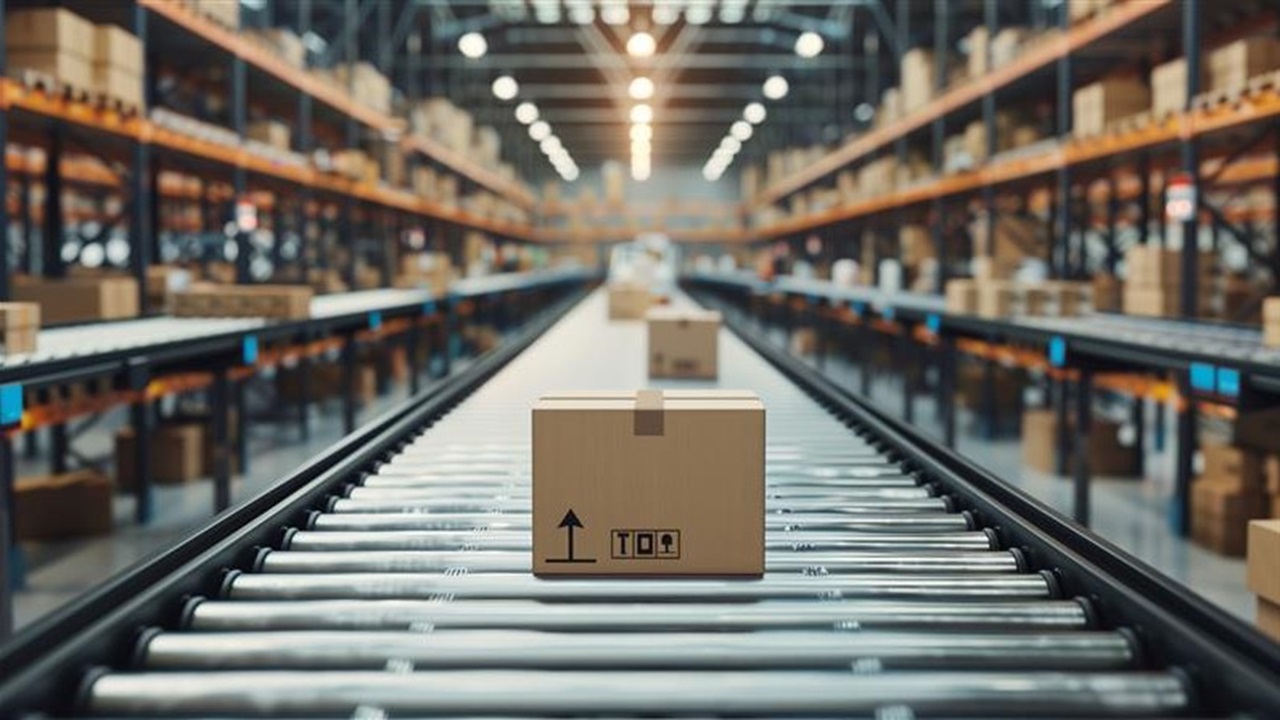
A distribution center desired to reduce maintenance time for conveyor belt replacement on its live roller conveyor, which transported a high volume of parcels. As one of the world's largest retailers, the customer sustained huge production losses for each minute of downtime. Naturally, the customer had aggressive operational goals to increase uptime and throughput and therefore needed to improve the speed and accuracy of conveyor belt replacements.
To cut maintenance for belt replacement, the customer required a faster means of joining the belt with a lower chance for error. Habasit satisfied this requirement with the PF-80/US joining press reduces the number of operations by replacing traditional screw-down pressurizing system with a simple lever mechanism. Additionally, the PF-80/US reduces the time of aligning the guiderail within the press by means of a notch that mates with the press frame. These design advantages reduce the error potential of improper pressurization and guarantee proper belt alignment during the joining process.
Once adopted, the PF-80/US hot pressing tool reduced both installation time and error rates.
Overall, the high-volume distribution center gained large savings by redeeming precious production time:
• Over 1 minute in time saved per belt joining
• $4,700 per minute in saved production
• A second corrective pressing operation due to faulty splice could cost an additional 25-30 minutes of downtime (or $117,500)
Savings reached at least $6,000 per belt join.
Additional time and costs are required when the operation is performed by an inexperienced operator. Multiple lines used the same live roller conveyor, so savings quickly multiplied. To help the customer meet its goals, the Habasit America engineering team designed and delivered the improved hot press in an urgent manner.