PNB-12EIWD with metal inserts for precise tracking
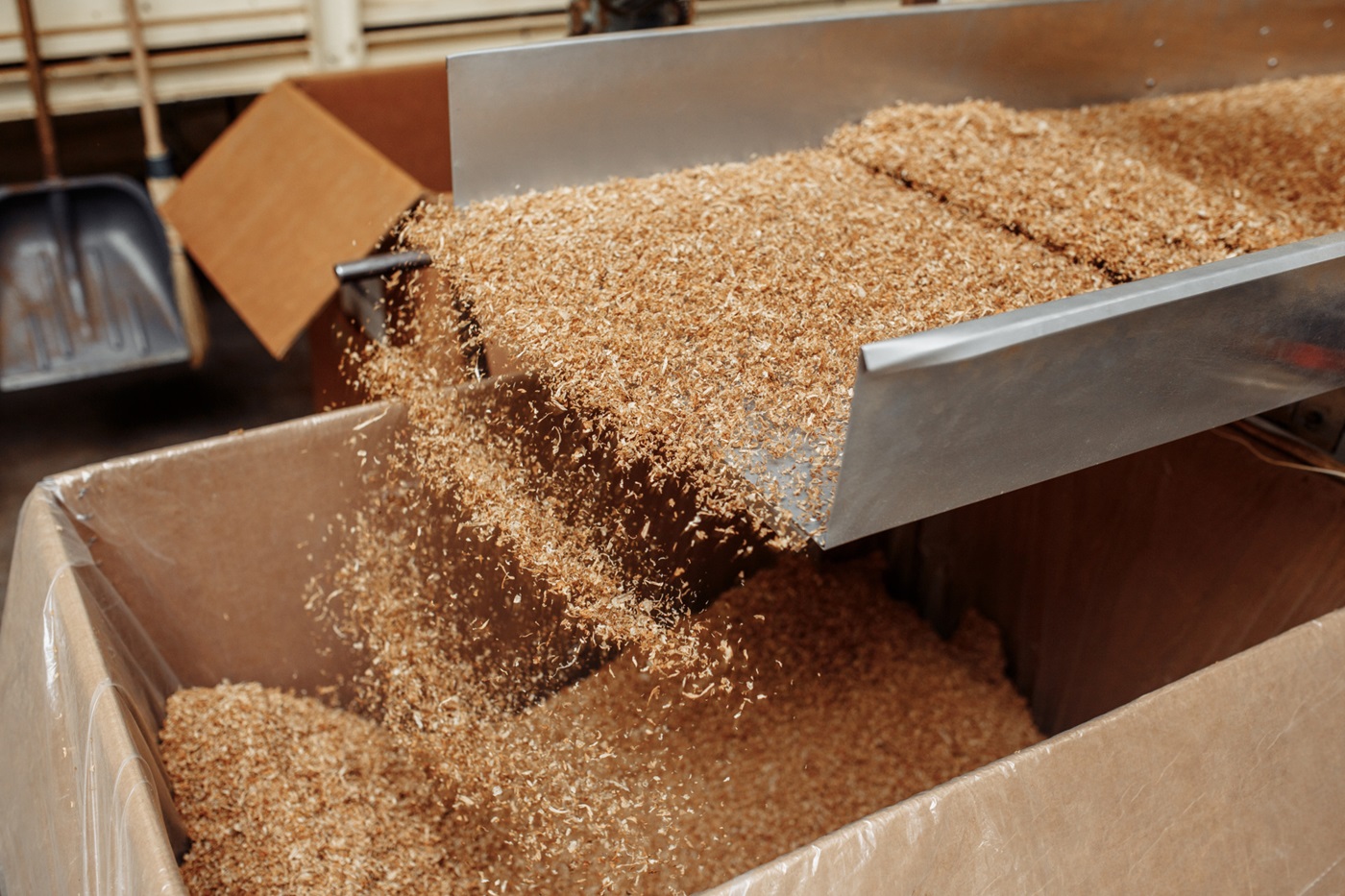
An international tobacco producer aimed for improvement on the weighing lines in Eastern Europe. The belt constantly moves tobacco through a set of pulleys with sensors to calculate the tobacco weight. To reduce belt vibration, a very precise fabrication with diagonal flexproof is required. Additionally, to improve tracking, metal inserts were welded on both belt sides and between belt layers. The scale is a very precise unit and requires top quality fabrication to avoid weighing mistakes that might be generated by a belt that is moving too much to the conveyor sides.
The customer needed a replacement belt with dimension stability, diagonal flexproof to run smoother on the returning pulleys, as well as metal inserts to improve tracking.
The installed belt PNB-12EIWD in one of the countries was working throughout the whole lifetime without tracking problems, in total about 3 years. The belt in another country in Eastern Europe is still running (one year after installation). An additional benefit is a smooth operation without any unpredicted breakdowns.
Overall, the customer experienced quick delivery and joining on-site to reduce scheduled maintenance break. Before, it was not possible to change the belt without demounting the whole scale, which took at least one to two days for operation and scale calibration. With the service team, the process could be decreased to 4 hours.