Lateral strength and surface frictions overcome mistracking and damage
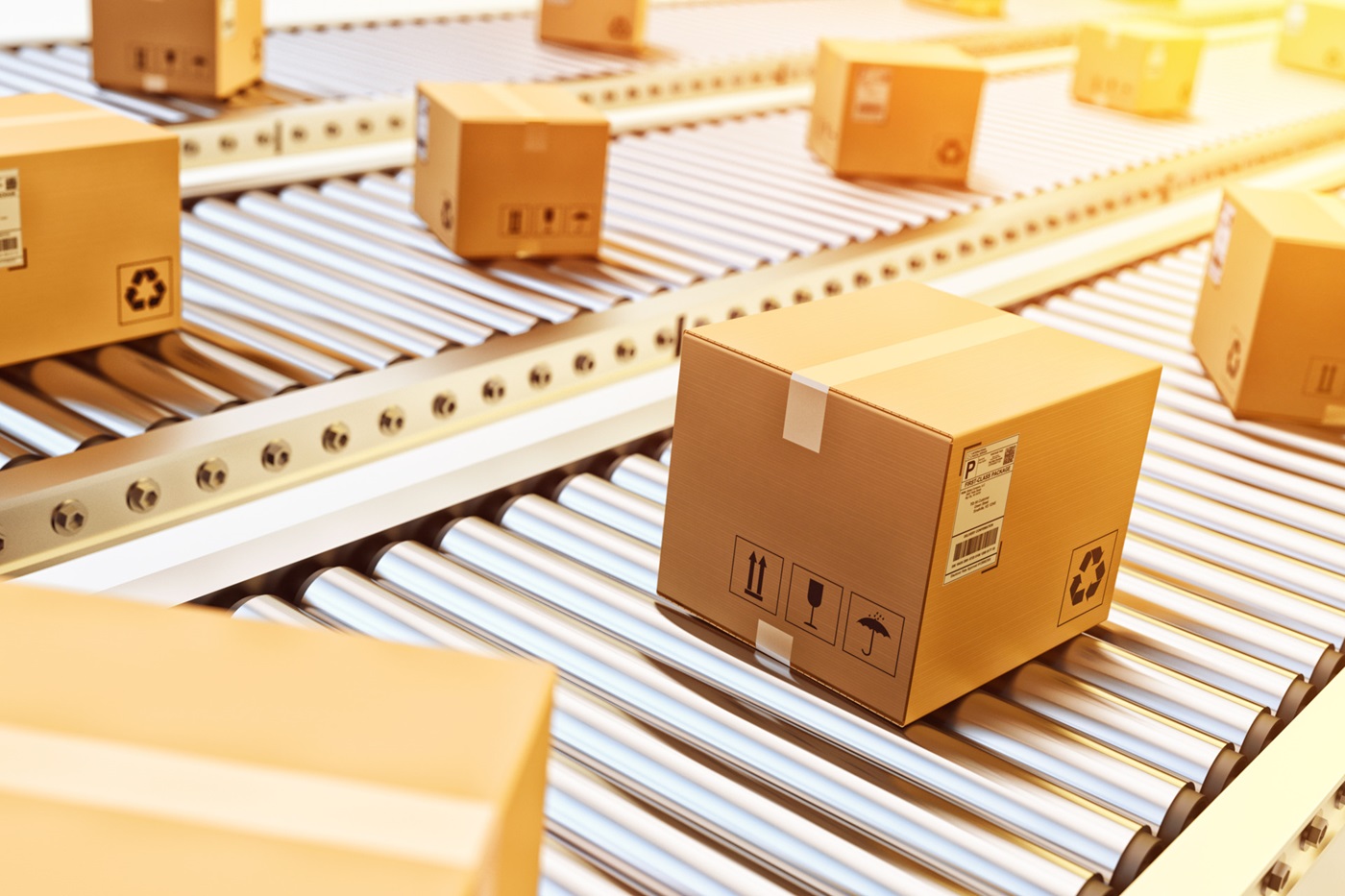
A distribution center desired a simple skewed roller design in order to align parcels to one side of its live roller conveyor. However, the belts that drove the rollers from underneath would mistrack due to the lateral force created by the skewed rollers, causing the belt to run against the edge of the conveyor and resulting in belt damage and failure. As a consequence, sections of skewed rollers could not be implemented, and instead, large capital purchases were required for additional equipment to achieve the desired case positioning.
To eliminate the harmful mistracking, the customer required a belt with higher lateral rigidity and friction lower on one side than the other. The TMPH90MFOXB features a medium friction orange peel cover, which pressed against the pressure rollers, while the higher friction running side pressed on the underside of the roller bed. The belt's more substantial design resisted mistracking and edge damage.
When installed, the TMPH90MFOXB enabled the use of skewed rollers and eliminated the need for auxiliary equipment to position the parcels.
Overall, the distribution center enjoyed huge savings by adopted the TMPH90MFOXB belt:
• $1,800 in diverting equipment per conveyor
• 300 conveyors in all equipped with skewed rollers
• Reduction in service calls to repair / replace belts
Total annual savings surpassed $500,000.
Through an inventive blend of surface texture and lateral strength, the TMPH90MFOXB allowed the customer to perform an "application we couldn't do before." The customer experienced a reduction in equipment cost and an improvement in reliability.