The World in a Can
When it comes to the world of cans, prepare for the unexpected. Whether it is the whole chicken coated in gelatinous gravy squeezed into a 50-oz can, roasted crickets with eggs, bacon with a decade long shelf life or a tin stuffed with an American cheeseburger, there seems to be no end to the culinary creativity of what you can put into a can. Even beverages are not limited to the average soda or beer. In China, you can buy a can of Bird`s Nest drink, a specialty made by dissolving Swiftlets` nests into a liquid which promises to stimulate cell growth and strengthen the immune system.
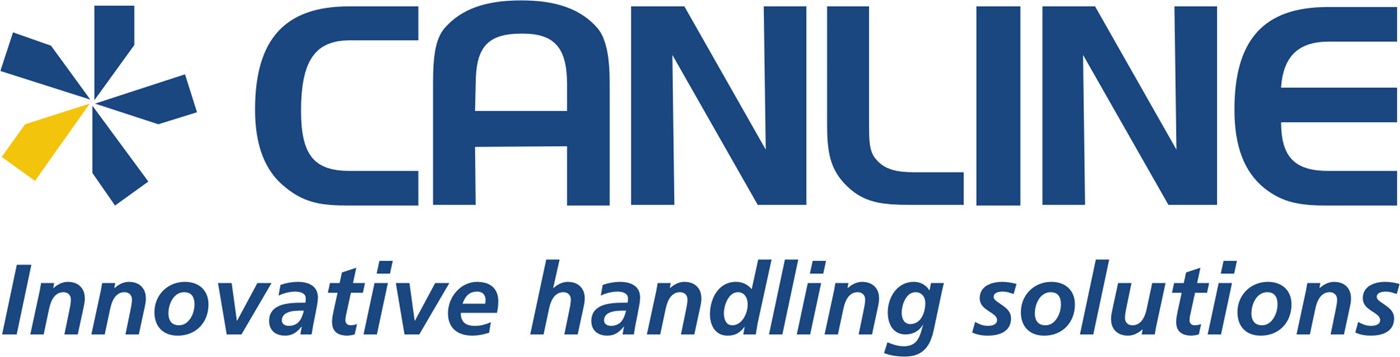
“In my opinion, you can put everything into a can,” says Mark Veron, Head of Technological Engineering and Development at Canline, and apparently, we do. In beverages alone, the world goes through approximately 180 billion aluminum beverage cans every year, so it should come as no surprise that there is a booming industry behind the ubiquitous can.
Changing forms
Based in the Netherlands, Canline is a Dutch international company who designs and installs turnkey transport and handling solutions for the metal and aluminum packaging industry. Using the technology of magnetism, vacuum, and air, Canline specializes in the internal transport that goes behind the making of the fragile but resilient can, an item which must be conveyed at high speeds without dent or damage. For this internal transport the company often uses Habasit fabric belts. Besides the close cooperation with Habasit at an early stage of engineering the machines and production lines, Canline also benefits from Habasit’s global service network.
With experience dating back to 1969, Canline has witnessed dramatic changes in the industry. The first aluminum can was created in 1957, followed shortly by the addition of the ring-pull in 1962 and the soda vending machine in 1965. When ring-pulls became a littering problem, not to mention a danger to animals and young children, the attached soda tab was invented in 1975, and the developments did not stop there.
“In the past production lines fabricated just one can size,” explains Mr. Veron, “but now customers are requesting more flexibility in diameter and heights. The quality of the printing, the increase of the production speed and reducing the thickness of the material to save costs, make it more and more challenging to keep, or even increase the overall line efficiency.”
Yet one of the most significant challenges in the modern industry is an aesthetic one. Cans simply can`t compete with the glamorous curves of a PET bottle. “Aluminum is more difficult to form,” says Mr. Veron, “The technique is there, but it is expensive and production speed is low.” Production rates can be as high as 3,000 cans per minute, but when a special form is being manufactured, it can slow down to half that speed or even less. Mr. Veron believes it will only be a matter of time before the industry finds a way to manufacture a more attractive can.
The healthy choice
In the past, canned goods have often had a reputation as the food we turn to as a last resort, but there are actually health benefits to this form of conservation. Many minerals and fat-soluble vitamins, such as A, D, E and K are preserved, not to mention protein and long-lasting fat (see gelatinous chicken). In some cases, the heat used in the canning process even brings out more antioxidants in vegetables like corn and tomatoes.
The other little known advantage is that the contents are often harvested and canned at their peak freshness, so although the shelf-life of a can of vegetables can be at least five years long, the food will, in the end, have more nutritional value than the slightly wilted vegetables at the bottom of your refrigerator.
Preserving the world one can at a time
Although canned food and beverages can be a practical, healthy and even appetizing choice, there is one benefit that outweighs them all, and that is sustainability. Aluminum is a material that can be recycled indefinitely. When you throw a can into the recycling bin, it will normally be transformed into a new product which will appear back on the shelf within 60 days of disposal.
“It is the most sustainable packaging in the world,” explains Mr. Veron. “If you want to recycle plastic, you always need to add new chemicals or material, but with steel or aluminum cans, they can be recycled up to 80 or 95%.” Although aluminum has immense recycling potential, the challenge is getting the can from the consumer`s hand to the recycling bin. It is worth the effort since creating a can from recycled aluminum saves 92% of the energy necessary to make a new one. In the United States, less than half of aluminum cans are recycled, wasting enough energy to maintain the electricity of more than one million homes for a year. Germany, Switzerland, Norway, and Finland do much better by recycling more than 90% of aluminum containers.
For the waste industry, plastics, even when recycled, can become a nightmare to separate. “It is simple to sort out aluminum by using the magnetic Eddy Current effect,” explains Mr. Veron, “but with plastics, there are six or seven different types so what is recycled becomes a milky stream which must be separated, cleaned, and regenerated before a new virgin material is added.”
Mark Veron believes that people are only now starting to recognize the sustainability of the can, but that it will have a huge impact on the future of recycling.
From the minute details to the masses
Canline has consistently been on the forefront of can engineering. Innovative development is a must in an industry with a future always more inventive than its past. Canline offers unique turnkey solutions, such as their latest exclusive machine called the Randomizer, which spreads the position of the cans` tabs during production to ensure easier and more even packing, while also reducing transport and storage costs. Details like this make a dramatic difference when thousands of ends are being produced by the minute. Even with the staggering numbers of mass global production, Mr. Veron expects further growth in the industry as people come to recognize the benefits of a can. When it comes to a sustainable future, culinary creativity is not all that may surprise you. (ST)
www.canline.com
Changing forms
Based in the Netherlands, Canline is a Dutch international company who designs and installs turnkey transport and handling solutions for the metal and aluminum packaging industry. Using the technology of magnetism, vacuum, and air, Canline specializes in the internal transport that goes behind the making of the fragile but resilient can, an item which must be conveyed at high speeds without dent or damage. For this internal transport the company often uses Habasit fabric belts. Besides the close cooperation with Habasit at an early stage of engineering the machines and production lines, Canline also benefits from Habasit’s global service network.
With experience dating back to 1969, Canline has witnessed dramatic changes in the industry. The first aluminum can was created in 1957, followed shortly by the addition of the ring-pull in 1962 and the soda vending machine in 1965. When ring-pulls became a littering problem, not to mention a danger to animals and young children, the attached soda tab was invented in 1975, and the developments did not stop there.
“In the past production lines fabricated just one can size,” explains Mr. Veron, “but now customers are requesting more flexibility in diameter and heights. The quality of the printing, the increase of the production speed and reducing the thickness of the material to save costs, make it more and more challenging to keep, or even increase the overall line efficiency.”
Yet one of the most significant challenges in the modern industry is an aesthetic one. Cans simply can`t compete with the glamorous curves of a PET bottle. “Aluminum is more difficult to form,” says Mr. Veron, “The technique is there, but it is expensive and production speed is low.” Production rates can be as high as 3,000 cans per minute, but when a special form is being manufactured, it can slow down to half that speed or even less. Mr. Veron believes it will only be a matter of time before the industry finds a way to manufacture a more attractive can.
The healthy choice
In the past, canned goods have often had a reputation as the food we turn to as a last resort, but there are actually health benefits to this form of conservation. Many minerals and fat-soluble vitamins, such as A, D, E and K are preserved, not to mention protein and long-lasting fat (see gelatinous chicken). In some cases, the heat used in the canning process even brings out more antioxidants in vegetables like corn and tomatoes.
The other little known advantage is that the contents are often harvested and canned at their peak freshness, so although the shelf-life of a can of vegetables can be at least five years long, the food will, in the end, have more nutritional value than the slightly wilted vegetables at the bottom of your refrigerator.
Preserving the world one can at a time
Although canned food and beverages can be a practical, healthy and even appetizing choice, there is one benefit that outweighs them all, and that is sustainability. Aluminum is a material that can be recycled indefinitely. When you throw a can into the recycling bin, it will normally be transformed into a new product which will appear back on the shelf within 60 days of disposal.
“It is the most sustainable packaging in the world,” explains Mr. Veron. “If you want to recycle plastic, you always need to add new chemicals or material, but with steel or aluminum cans, they can be recycled up to 80 or 95%.” Although aluminum has immense recycling potential, the challenge is getting the can from the consumer`s hand to the recycling bin. It is worth the effort since creating a can from recycled aluminum saves 92% of the energy necessary to make a new one. In the United States, less than half of aluminum cans are recycled, wasting enough energy to maintain the electricity of more than one million homes for a year. Germany, Switzerland, Norway, and Finland do much better by recycling more than 90% of aluminum containers.
For the waste industry, plastics, even when recycled, can become a nightmare to separate. “It is simple to sort out aluminum by using the magnetic Eddy Current effect,” explains Mr. Veron, “but with plastics, there are six or seven different types so what is recycled becomes a milky stream which must be separated, cleaned, and regenerated before a new virgin material is added.”
Mark Veron believes that people are only now starting to recognize the sustainability of the can, but that it will have a huge impact on the future of recycling.
From the minute details to the masses
Canline has consistently been on the forefront of can engineering. Innovative development is a must in an industry with a future always more inventive than its past. Canline offers unique turnkey solutions, such as their latest exclusive machine called the Randomizer, which spreads the position of the cans` tabs during production to ensure easier and more even packing, while also reducing transport and storage costs. Details like this make a dramatic difference when thousands of ends are being produced by the minute. Even with the staggering numbers of mass global production, Mr. Veron expects further growth in the industry as people come to recognize the benefits of a can. When it comes to a sustainable future, culinary creativity is not all that may surprise you. (ST)
www.canline.com