HabasitLINK SE620 Flush Grid with Stainless-Steel Rods Solves Swelling Issue & Preserves Belt Life
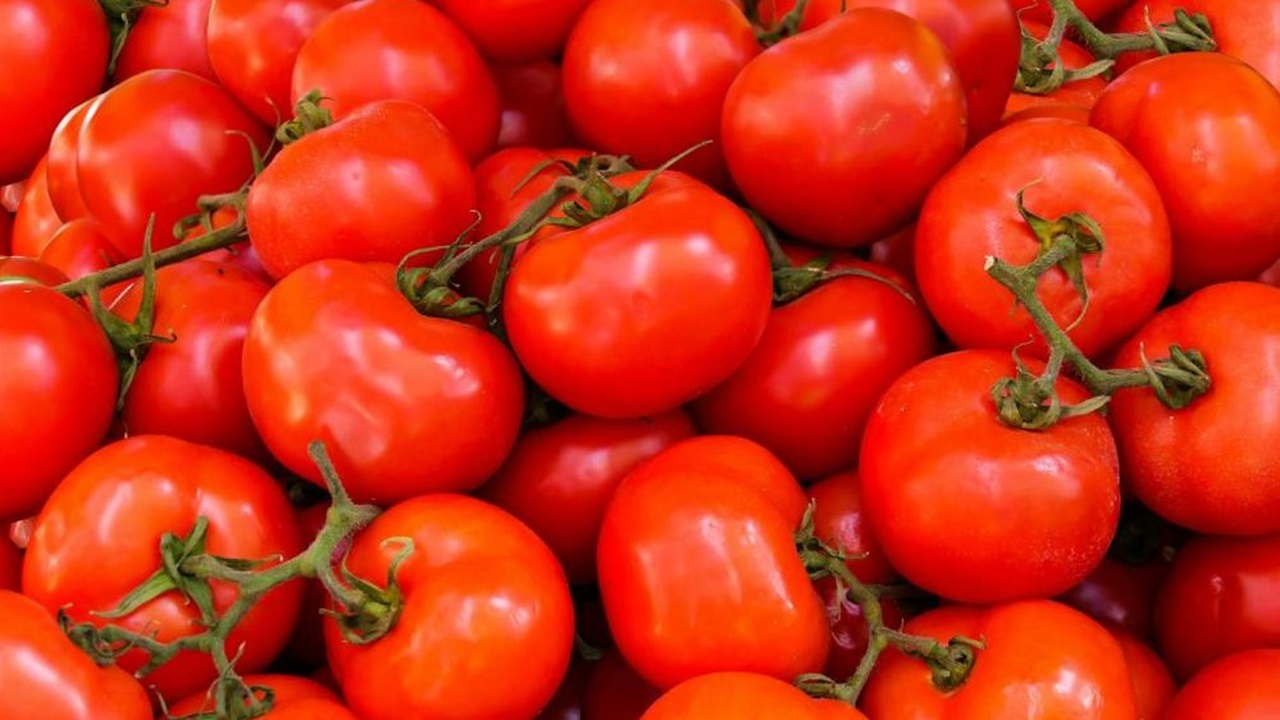
Turning tomatoes into paste is a large business in California’s central valley. As part of processing products during harvest season, a large commercial tomato farm moves tomatoes from a washer to a steamer. This application is high-volume and runs 24 hours a day for four straight months.
The process allows for a high volume of water to come into contact with the modular belt and the nylon rods. Saturating the nylon rods caused rod swelling, creating a binding effect on the belt and eventually causing belt failure.
Due to the critical nature of the belt in the process, the company could not afford a breakdown in the middle of the season, thus creating the need to buy a new belt every year. Belt maintenance, belt replacement, delays in production and the labor to make the changes made this one of the most expensive replacement items in the plant.
After evaluating their options, the customer opted for Habasit’s SE620 Flush Grid modular belt with special stainless-steel rods. The more robust SE620 modules, coupled with the stronger stainless steel rods, made the conveyor impervious to the excessive amount of water and minute articles of sand that was also creating a wear pattern on the softer nylon rods.
With the new Habasit belting solution, the tomato producer can now:
- Get a minimum of three additional harvest seasons from each belt.
- Significantly reduce the labor hours needed and the associated costs of the typical maintenance on this belt.
- Minimize line interruptions due to inferior modular designs.
Savings: $23,716 based on total belt savings and belt installation savings.