Habasitlink M2533 Saves a Lot of Bread for Sandwich Maker
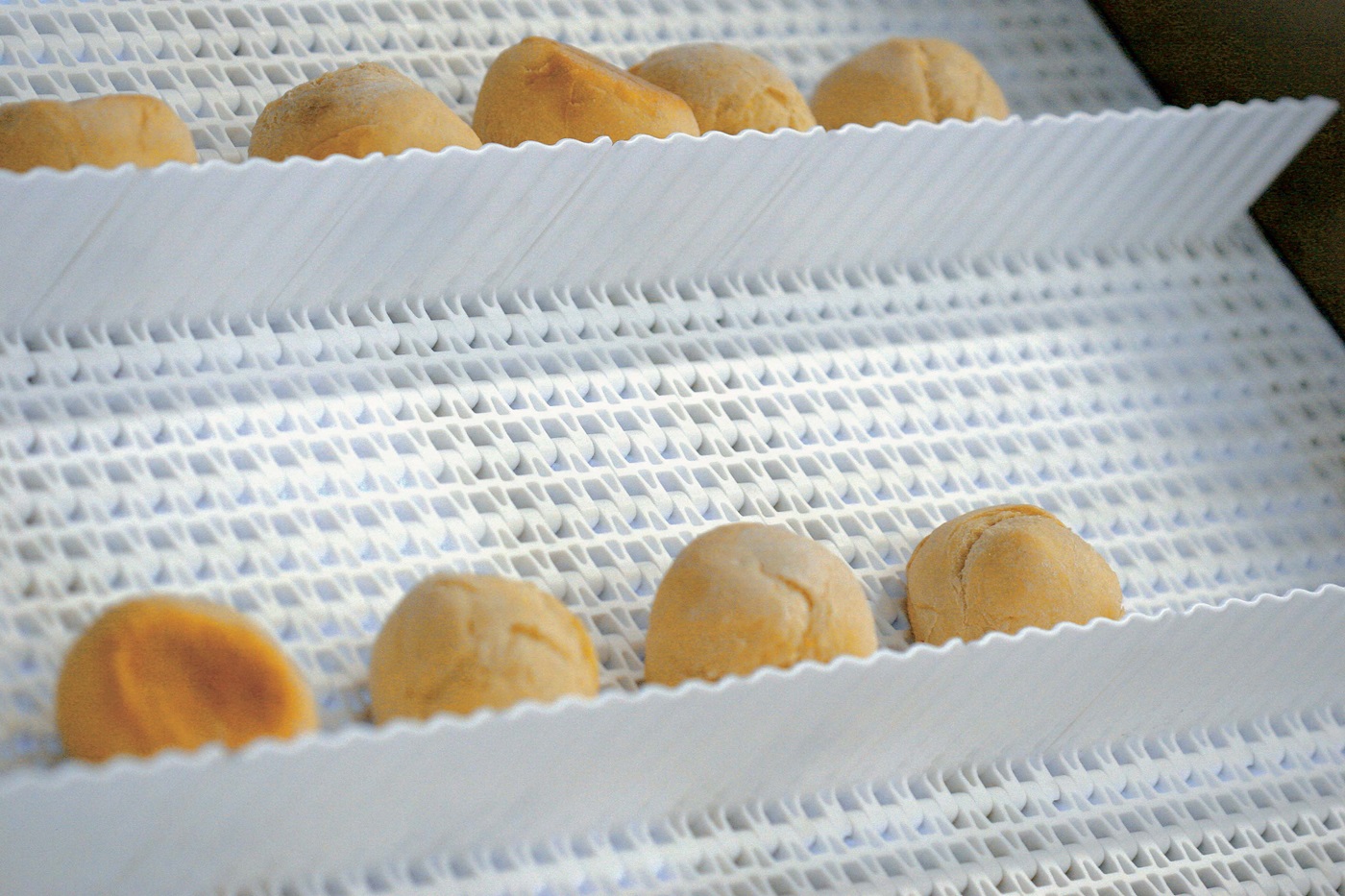
To make sandwiches fast, a food company moves open-faced deli buns along a conveyor where meat and other ingredients are added. In the past, the bread often fell onto the floor or shifted out of the loading position. Lots of product toppings ended up in the waste bin, and extra personnel had to be placed along the line to keep the buns stabilized to receive the garnishes. Habasit developed a cost-effective alternative featuring a 14-inch-wide HabasitLINK M2533 with four lanes of 5-inch long side guards, cleats on 12-inch centers and flights to properly hold the buns. This design made it possible to secure and position each bun so that production workers could easily and neatly place the ingredients on them.
Within a few months of implementing the new belt, the client reported some meaty results:
- Higher food production: workers no longer have to stop the belt to reorient the buns
- Dramatic drop in product waste
- Reduced cleanup- and safety-related downtime
- One fewer staff member needed per shift; now available for other duties
The total savings achieved since making the switch: $1,204,488 based on decreased labor for production, reduced loss from product damage and maintenance savings.