HDS605 TT’s Low-Temperature Handling
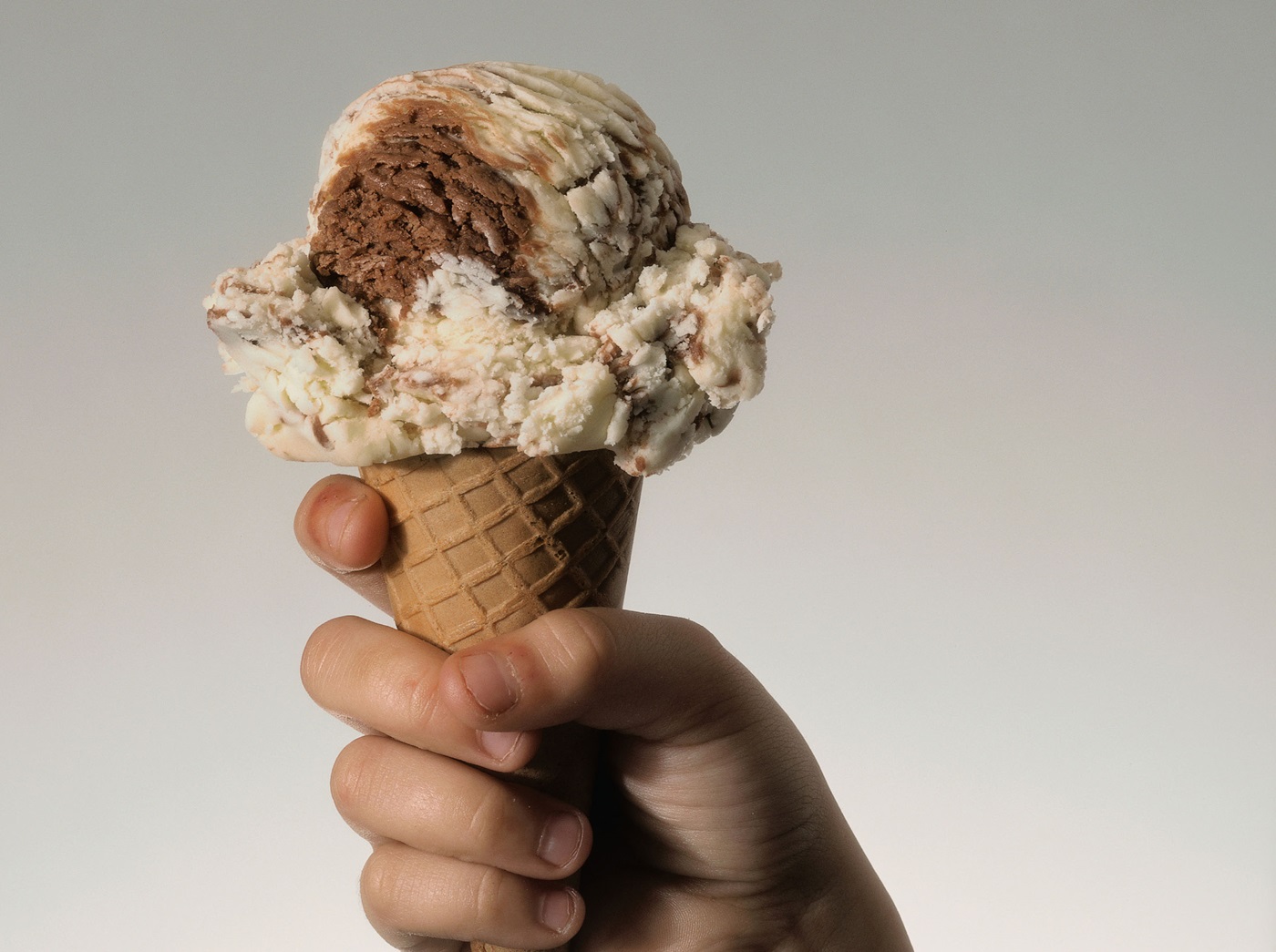
A novelty ice cream manufacturer was using a urethane belt rated at -10ºF to move frozen treats to the packaging line. But the frigid air from the freezer was causing frequent belt cracking and slipping on the rollers. And, the ice cream was sticking to the belt’s fabric.
These challenges required maintenance personnel to oversee the line for sixteen hours a day, ultimately resulting in $2k per week spent watching the belt for crashing, sticking and mistracking. To eliminate this costly supervision and maintenance, the customer needed a belt that could withstand the freezer’s -40ºF temperature and provide positive drive with less product build-up.
Habasit retrofitted to a plastic modular belt of polyurethane material—the HDS605 Texture Top. The belt’s material solved the temperature challenge, while the positive drive solved the tracking issue and its texture solved the sticking problem.
Where the original urethane fabric belt would only last a couple of months, even with constant maintenance involvement, the HDS605 TT has been running for over 1.5 years with no issues. Now, not only does the customer no longer need someone on standby, but they don’t have to replace the belt every two months.
Total annual savings include $100k.