Durable Construction of Habasit Cleandrive Resists Damage From Nearby System Parts
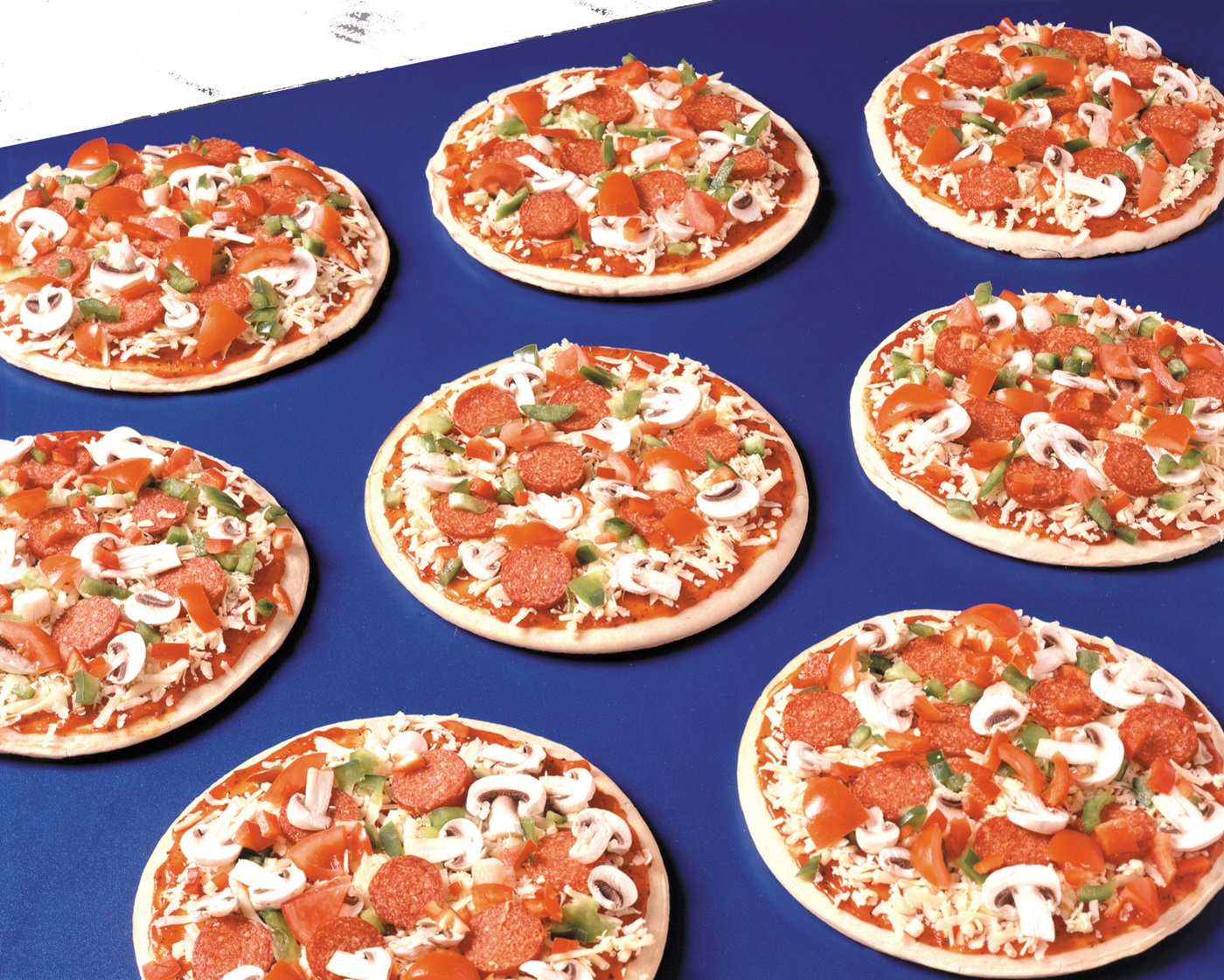
A frozen pizza manufacturer was conveying finished product and diverting it along the line with a powered belt diverter. Because of the proximity of the diverter belt to the transport belt, the diverter belt’s edges were getting damaged, causing pieces to come loose and contaminate the product. In some cases, strings from its edges would also get entangled in system components. The time spent fixing these belts resulted in ~6,800 units of lost production—not including those that were contaminated.
The company needed a belt with more durable edge construction to resist dynamic contact between the two belts and other conveyor parts. So, Habasit replaced each diverter belt with the Habasit Cleandrive Friction Drive Belt. Its polyurethane body with fully embedded tensile cords is designed to eliminate belt particle release and tensile yarn stringing that may interfere with machine components.
This change significantly reduced the customer’s contamination risk, product loss, potential for recall and unexpected expenditures. It also improved their uptime and preventative maintenance predictability. The new belts have now been in production for nine months with no issues!
Total annual savings of $97K.