Heavy-Duty M2670 Proves Strong Enough for Razor-Sharp Car Panels
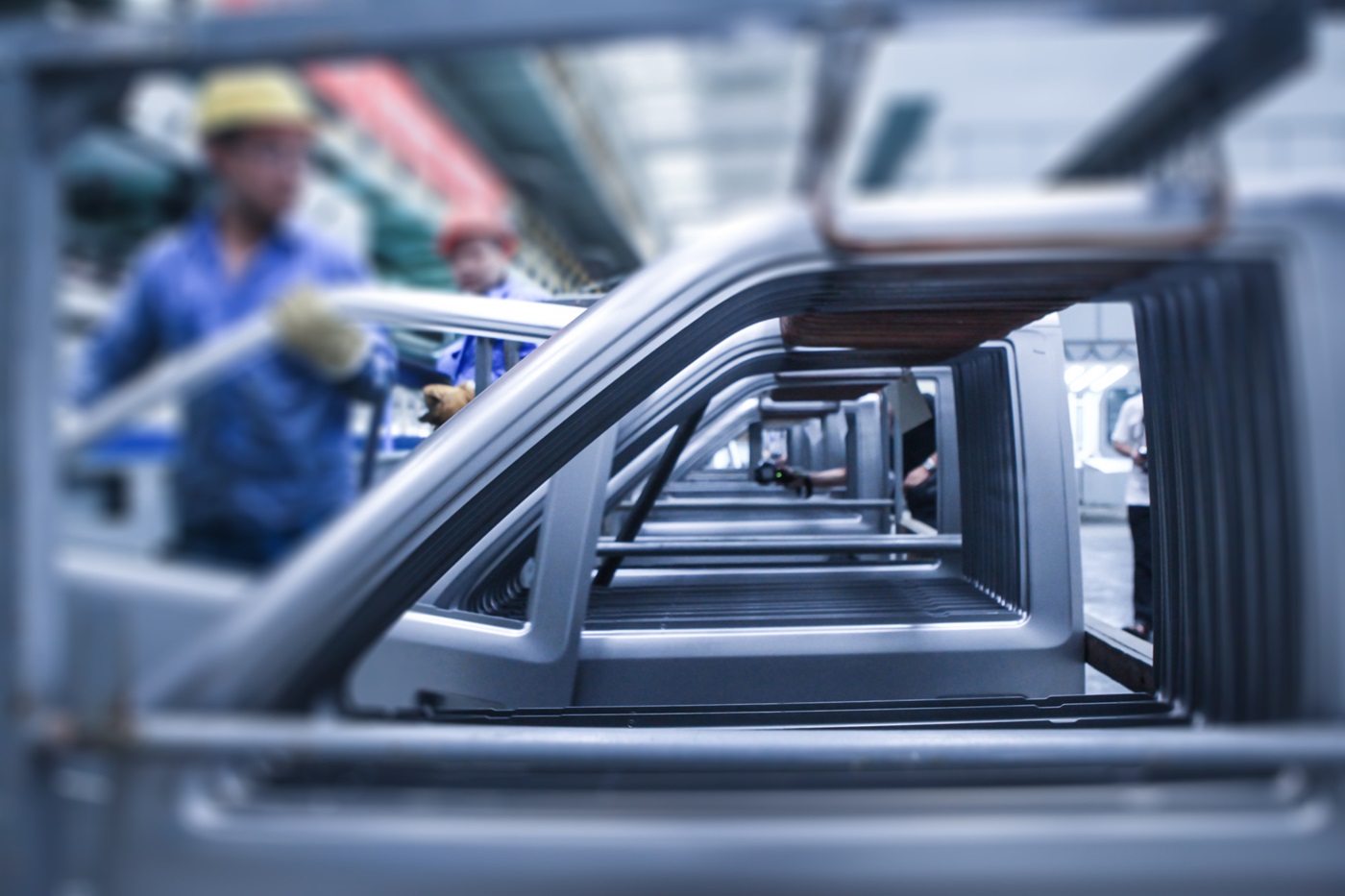
A large automotive manufacturer struggled with continual belt repairs due to the razor-sharp edges of car panels, which were dragged off the panel delivery conveyor by hand, puncturing and tearing the existing fabric belt. Frequent maintenance was required to preserve the belt, but ultimately, a full replacement occurred every three to six months.
To combat the expensive and belt-compromising damage, the manufacturer required a heavy duty, wear-resistant belt to minimize punctures and tears. Habasit satisfied this requirement by transitioning to a plastic modular conveying solution and installing the M2670 Flat Top Heavy Duty 1" belt. The belt's natural strength and stiffness are maximized when produced in acetal (POM), which also enjoys a lower friction surface, better facilitating the dragging of the sharp-edged panels.
The M2670 proved to be transformative in this application, eliminating the constant belt repair and maintenance, which accumulated high labor costs and production losses. The sharp panels slid on the durable, low-friction surface with relative ease.
Making the switch delivered enormous results:
- Curtailing belt repairs saved approximately $10,000 per week
- Longer lasting belting reduced replacements for savings over $70,000 per year
Estimated annual savings surpassed $550,000.
Due to performance, the M2670 became the specified belt in all stamping plants for this automotive manufacturer.