Secure Rods and Sturdy Modules Slash Costly Unscheduled Downtime
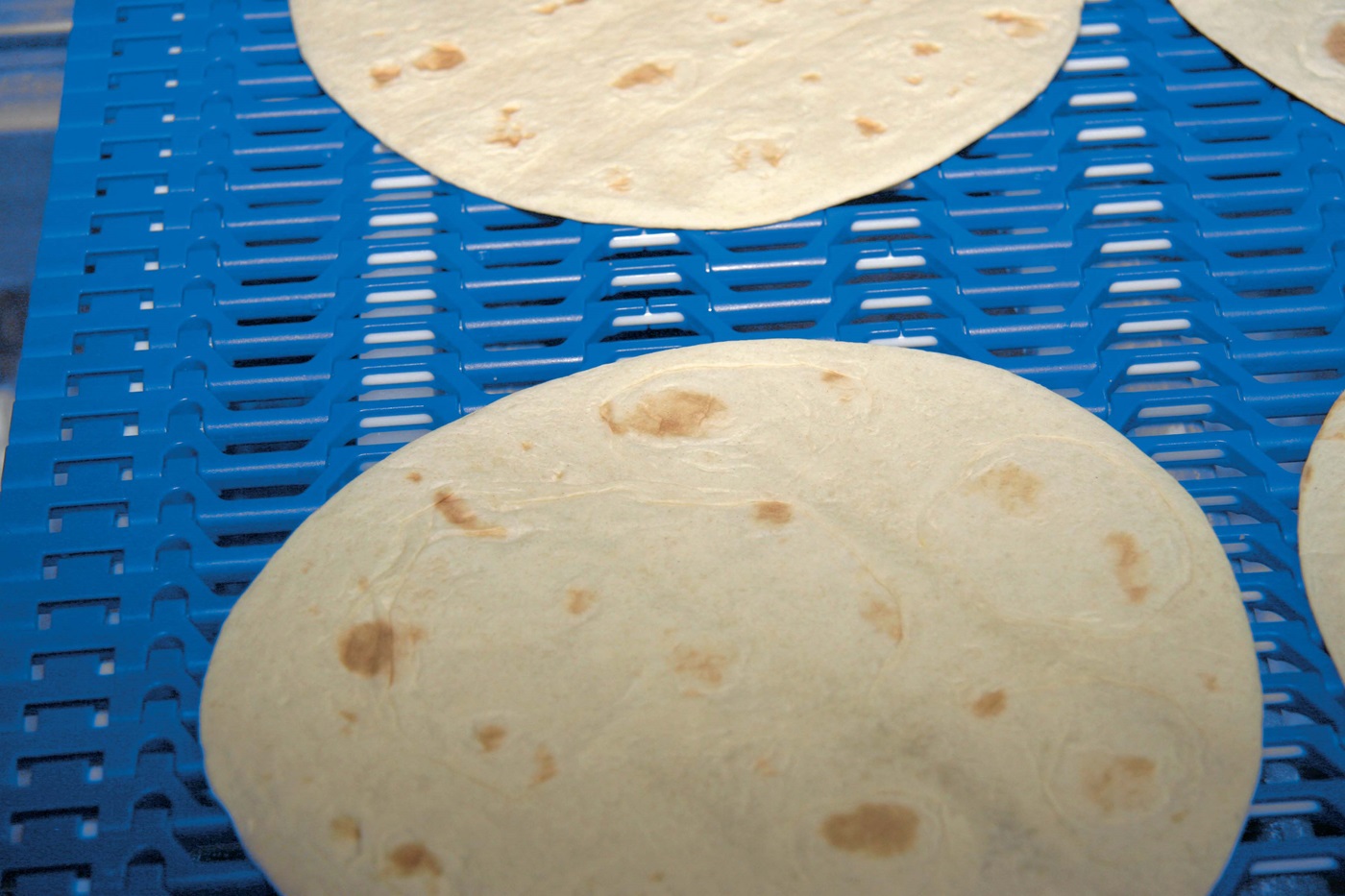
One of the world's largest producers of corn flour and tortilla products suffered unscheduled downtime in its tiered cooling conveyors due to two recurring problems with a competitor's belt: rod migration and edge module breakage. Rod positioning depended on an unreliable friction fit, and the edge modules featured a structurally weak, hollow-like tip design. As rods loosened and modules broke, this producer absorbed large costs in both maintenance labor and production losses. To overcome the design issues and resulting down-time, the producer required a plastic modular belt suitable for conveying tortillas in a tiered cooler with no rod migration and edge module breakage. Habasit satisfied these requirements with the M1185 plastic modular belt, which features Smart Fit rod retention technology and robust edge module design. Smart Fit rods have a molded retainer ring that secures the rod in place, and each rod head is positioned to support to the sturdy edge module tips. The M1185 performed with no rod migration and module breakage, eliminating all related downtime. Additionally, the competitor's friction-fit rods offered no advantage in disassembly as Habasit's Smart Fit rods are easily removed and reinserted.
Due to high production volume, each hour of down-time created large costs for the producer, making the M1185 a high-value solution:
- Annual belt savings amounted to $6,925
- Reduced maintenance labor due to unscheduled downtime saved $3,840 annually
- Performance-related production losses were eliminated, achieving savings of $109,200
Estimated annual savings surpassed $119,965.
After switching to Habasit's blue M1185 belt, the producer enjoyed greater visibility of the tortillas during production, gaining additional value over the competitor's tan option.